New knowledge can provide improved recycled aluminium
Recycling cast aluminium saves a lot of energy. But there is potential for increased reliability and strength. In a new PhD thesis from School of Engineering at Jönköping University, Anton Bjurenstedt has found some of the missing puzzle pieces.
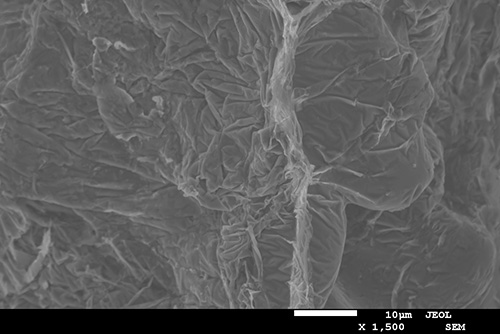
SEM photograph of the fracture surface of a tensile test specimen
Working in a material lab, Anton Bjurenstedt was often tasked with finding out why a cast component had broken. But nobody asked how to prevent the same thing from happening again. When given the opportunity, he applied for a PhD position at School of Engineering, Jönköping University, to get a deeper knowledge on what factors deteriorated the strength of recycled cast aluminium.
The automotive industry, a major user of cast components, must recycle 95 percent of the weight of a car. Furthermore, the production of recycled aluminium can save a lot of energy; as little as 5 percent of the energy used to produce new aluminium is needed when recycling. But today, recycled aluminium is usually not used in components where high security is required, because it doesn’t have sufficient strength and reliability.
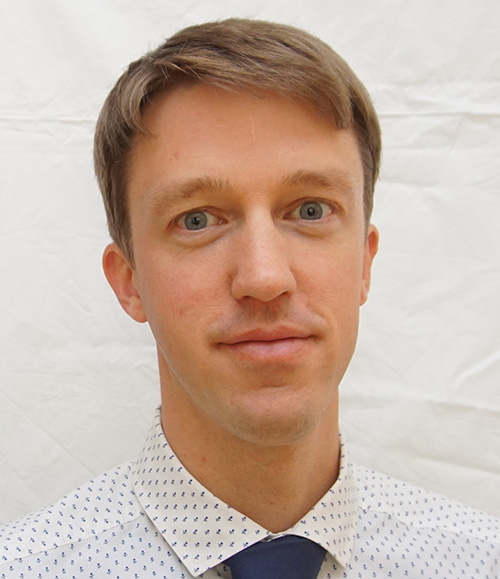
“When mixing and melting different kinds of scrap, there is a risk that it will contain more and more iron. It's like mixing salt in water; It is only possible to dissolve a certain amount before clumps are formed. At high temperatures, the iron is dissolved in the aluminium, but when it solidifies, it forms what we call iron-rich phases, microscopically small collections containing iron in the material”, Anton Bjurenstedt explains.
By understanding how the iron-rich phases are formed, how they grow and how they affect mechanical properties, recycled cast aluminium can be made more useful. And in the slightly longer term, they may even contribute to increasing the strength of the material. Anton Bjurenstedt has carried out experiments where, with the help of x-ray equipment, he could see in real-time how the iron-rich phases formed when the aluminium solidified. He has also carried out tensile tests in scanning electron microscope and investigated fracture surfaces and fracture profiles.
Among other things, he discovered that if, for example, manganese or chromium was added, the shape of the iron-rich phases changed, they formed more easily and distributed less homogenous in the material.
Aluminium oxide is another problem that is addressed in the thesis. It is easily formed on the surface of molten aluminium, much like a thin fabric that sits on top of a dough. When the “dough” is mixed, the “fabric” is pulled into the mixture and forms creases. Between the “fabric” and the “dough” the adhesiveness is good, but in the folds, the material does not bind together.
“The problem with oxides is that they can’t be measured”, says Anton Bjurenstedt. “Most agree that they decrease the strength of the material, but no one has been able to find the correlation.”
Anton Bjurenstedt successfully defended his thesis On the influence of imperfections on microstructure and properties of recycled Al-Si casting alloys on 15 September.
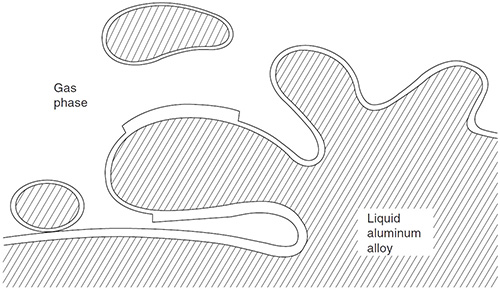
Oxides retain their bonding to the liquid aluminium, but between the two dry surfaces there is no bonding and the entrained oxide will act as a crack in the melt.
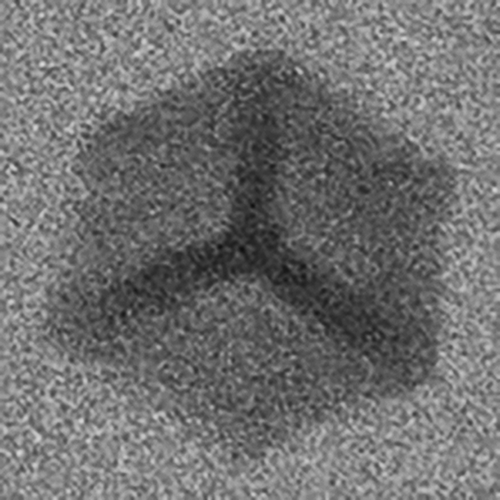
Microscopic iron-rich phase in aluminium